Entries tagged with “welding”.
Did you find what you wanted?
Mon 1 Dec 2014
Posted by admin under ACGIH, Air Monitoring, Chemical Exposure, Ethics, Exposure, Hazard Communication, hygienist, industrial hygienist, occupational hygiene, Ozone, PEL (Perm Exp Limit), Welding
Comments Off on Ozone during aluminum welding
Confession: I missed the assessment of this hazard the first time.
Awhile back I performed air sampling during aluminum welding. The welders were cordial and let me crawl over their welding equipment, poke around old boxes of wire and metal stock. I did not think there were any “real” hazards. We did find some airborne levels of various metals. From the picture can you tell who did the most welding?
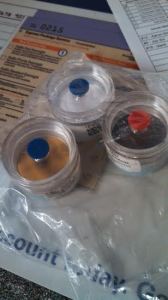
After I had performed the sampling and the report was sent, I was asked if I had checked for ozone (O3)? I admitted I hadn’t and asked if it was an issue? Well, apparently it is (or rather, might be).
I went back to the shop, begged for another chance, and performed ozone sampling. It wasn’t difficult, but eating crow was the hardest part.
More information on the subject can be found at: NIOSH, UK- HSE. Ozone is formed when the UV radiation hits oxygen. The ACGIH TLV is variable (see table below)
, and the OSHA PEL is 0.1 ppm.
Health: Ozone, O3, can cause lots of different respiratory illnesses. These can include a decrease in lung function, aggravation of asthma, throat irritation/cough, chest pain, shortness of breath, inflammation of lungs, and a higher susceptibility to respiratory illnesses. ACGIH classifies it as an A4, or not a suspected carcinogen.
Luckily the results were found to be non-detectable (“IH talk” for none-found). Which only means I didn’t find it, not that it is not there. I sampled for a long time (530 minutes) because they were working 10 hour shifts. But, they only welded for a total of approximately 1.5 hours during that time.
If welders are in a confined area, or a small space with limited ventilation, the results might be significantly different.
Fri 14 Feb 2014
This has to be one of the coolest types of cutting. Raw obliteration of metal.
As you know, hexavalent chromium (Cr6) is generated when the metal, chromium, is heated. Cutting this metal with a plasma torch is an easy way to heat it up quickly.  We performed air monitoring on one employee performing plasma cutting on #304 stainless. Luckily the employee was wearing a 1/2 face tight fitting respirator (and skin protection due to the body readily absorbing Cr6) and we found exposures at 36% of the exposure limits (they were within the acceptable limits). This employee was able to stand away from the cutting due to the machine he was using. He did not do this task all day and no engineering controls (ventilation) was used.Â
****Caveat: Please do your own air sampling. Conditions and environment may not be similar to your environment, and they can change rapidly. One sampling event rarely indicates all conditions. We’re talking about people’s health!****Keep in mind welding safety!Â
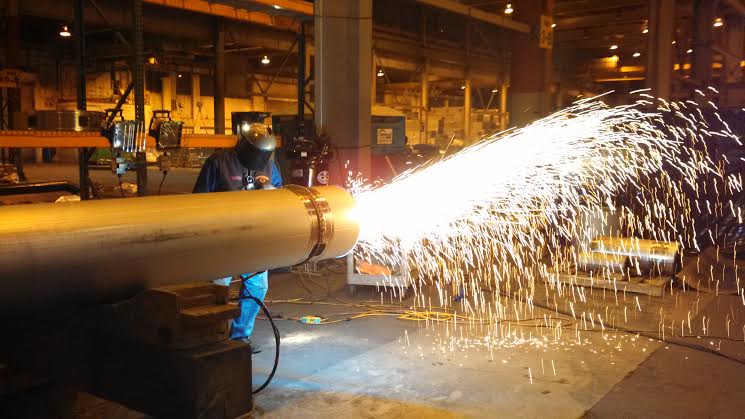
And a close up of the cutting machine without the motor & tracks:
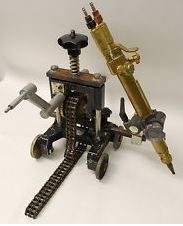
Wed 13 Feb 2013
Posted by admin under Chlorinated Solvent, confined space, Engineering Controls, Galvanized welding, Hexavalent chromium, Noise, Personal Protective Equip (PPE), Respirators, Risk, Stainless Steel, ventilation, Welding
Comments Off on Welding health & safety
I’m easily impressed with welding and welders. Welding looks so simple, yet hard, dangerous and permanent.
When interviewing your welder, here are some questions to ask: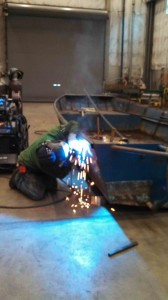
- What type of welding are you doing?
- What type of metal do you weld on? (mild steel, stainless, galvanized)
- Is there any coating on the metal?
- What type of flux is used?
- Where do you weld?, and then, “Where else?”
- Is there any ventilation in the area you weld?
- Are there any flammables in the area?
- Do you wear any PPE when welding? (ear plugs, respirator, leather)
- When do you use fall protection?
- Do you have & use welding shields?
What makes welding so difficult is the number of variables involved. The welding variables can change by the minute. Educate your employees on these dangers.
After the above questions, if the employee is agreeable, I ask some additional questions. These are the ones that provoke the best stories:
- What is the strangest things you’ve welded?
- Have you ever welding in a really small (confined) area?
- Have you ever welded with exotic metals? fluxes?
- What’s the worst thing you’ve welded on?
- Have you ever gotten sick from welding?
There are many, many more questions to be asked depending on the answers. The authority on this subject, Michael Harris, has written an excellent book on this subject, “Welding Health and Safety“(ISBN 978-1-931504-28-7). It is available from AIHA. It is VERY detailed, and money well spent if you do welding. I have taken his short course (all day) and I learned more than I ever thought possible, and I still can’t even weld!

Mon 2 Jul 2012
Posted by admin under Dermal, Hexavalent chromium, Management, Stainless Steel, Welding
Comments Off on Hardfacing – Chromium 6 – Picture of the day
If you use heavy equipment and need to move dirt, rocks or soil, look closely at the buckets. Many times they will be coated with a material called hardfacing. It is a durable (consumable) welding bead laid out in a pattern. This pattern (from what I am told) helps to extend the life of the bucket. Apparently the cost of putting this product on the buckets is well below the cost of replacing the bucket (or teeth, or whatever).
The hazard is really on during the application of hardfacing. See my earlier post here. Hardfacing contains stainless steel (approximately 25%?, but it varies). Heating the stainless steel releases chromium in it’s hexavalent form (Cr6).
If your buckets have this on their exterior, your employees are probably exposed to hexavalent chromium at some point in the year.
However, the pattern is an art & science. Look closely at the side of this bucket…I think I know where this welder got his inspiration.
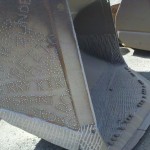
Tags: air monitoring, bucket, chrome 6, Chromium 6, cr6, excavator, hexavalent chromium, industrial hygiene, loader, safety, welder, welding
Mon 14 May 2012
If you hardface on construction equipment (or anything) you *probably* have overexposure to airborne hexavalent chromium. There are always exceptions, but if you are using a hardfacing wire/stick with any amount of chromium in it, the process (heat) generates hexavalent chromium. For how this happens, go here.
In construction it is quite common to have buckets and equipment with hardfacing applied to the surfaces in order to protect the equipment from excess wear and deterioration. The grid pattern varies
, but it can look like this.
I realize that the application of the hardfacing procedure doesn’t occur very often. However, when it does, there is usually high levels airborne hexavalent chromium generated. So, what to do?
- Use some type of ventilation system (I know, I know, it messes with the shield gas, but do something!)
- Wear (at least) a 1/2 face tight fitting respirator with P100 (HEPA) filters (honestly, I’d buy a powered air purifying welding hood if I was doing it..and money was not an object)
- Cover any exposed skin (it can be absorbed by your skin)
- Designate the area as hazardous and limit the activities in this area (no eating!)
- Perform air monitoring to verify airborne levels are below limits (and get an IH out to evaluate it)
These suggestions really only scratch the surface of what you should do. Doing all of the above will not even meet the OSHA rules…but it will help protect you from exposure. Here is the OSHA Fact Sheet. Â Another article from Welding Design & Fabrication.
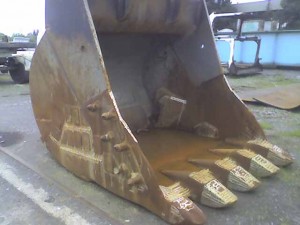