So, while standing in the California jet-way waiting to board my plane, I noticed this sign. It was most likely a Proposition 65 labeling warning. However, what in the world do you do with that information? How did posting that sign change any behavior? Could I have done anything different to avoid the jet fumes?
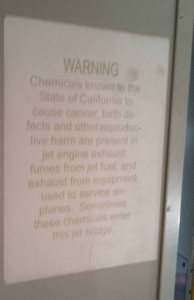
It reads, “Warning. Chemicals known to the State of California to cause cancer, birth defects and other reproductive harm are present in the jet engine exhaust fumes from jet fuel, and exhaust from equipment used to service airplanes. Sometimes these chemicals enter this jet bridge.”
In much the same way, sometimes our warning to employees is pointless. What can they do different? What is the point of telling them something if there is nothing we can do different?
The global harmonization system (GHS) is being implemented in the US by the end of 2013. By 2014 you must train your employees on the new changes to the (Material) Safety Data Sheets (SDS, now). (BTW, there are also some other things you must do).
The message I am trying to make (double irony, I know) is when you are training your employees, how do you measure the effectiveness If they “sign in and say they were in your training”, were you effective? Here are some suggestions, which might help to measure the right thing:
- Questions. This ___ number of the audience asked ___ questions.
- Feedback. I received ____ # of suggestions for the next training.
- Changes. They are going to implement ____ changes to their workplace.
- Secondary labeling. (GHS specific, of course) While walking around the site, I noticed ____ secondary labels with the new labeling pictographs.
I admit these aren’t the-best-suggestions-ever. But, warning someone without an alternative, method to change, or way to adopt a change, is really pointless.